PLANT FOR THE PROCESSING – LIQUEFACTION – OF COAL INTO SYNTHETIC HYDROCARBON FUELS BY THE METHOD OF PLASMA-CHEMICAL REACTION
The innovative production method is low-cost, environmentally friendly and promising in terms of the deep processing of coal into liquid hydrocarbons.
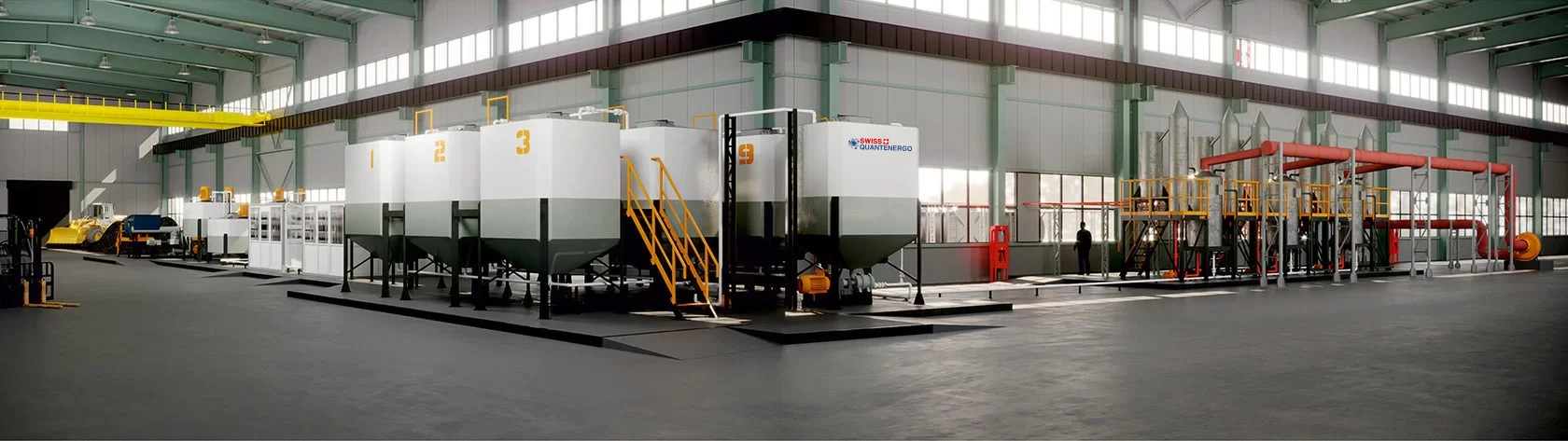
FACILITY LAYOUT SCHEME
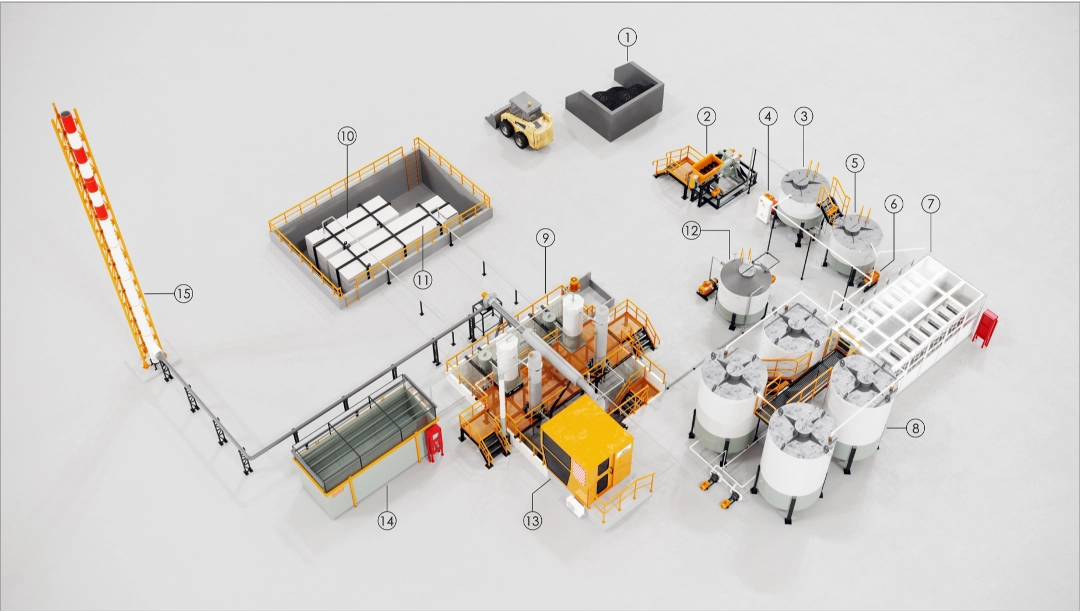
1 – Initial coal
2 – Wet grinding disintegrator
3 – Mixing container
4 – Cavitation hydraulic impact disperser
5 – Storage tank
6 – Pump
7 – Plasma chemical pulsed reactor
8 – Storage tank
9 – Plant for processing hydrocarbon fuel into straight-run gasoline, diesel,
low-temperature oils
10 – Storage tank for gasoline
11 – Storage tank for diesel fuel
12 – Storage tank for low temperature oil
13 – Control post
14 – Cooling tower
15 – Chimney
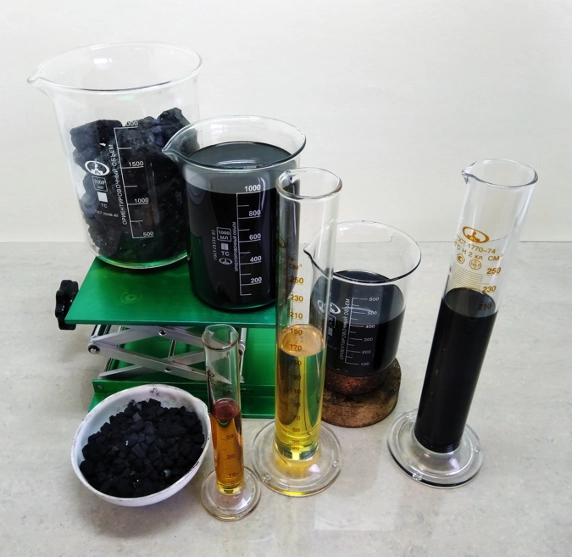
Coal-to-Liquids (synthetic hydrocarbon fuels)
The process of converting coal into synthetic hydrocarbon fuel is cyclically continuous. Its peculiarity is in the use of the obtained synthetic hydrocarbon fuel as a process catalyst as a solvent-activator.
Production is carried out at atmospheric pressure, without high temperatures, expensive catalysts and ‘additional hydrogen’; the only source of hydrogen is water.
From one ton of coal, 400 liters of hydrocarbon fuel (synthetic oil) are extracted, from which:
- gasoline fraction – 11% - 0.740 g/cm3;
- diesel fraction – 40% - 0.825 g/cm3;
- low-temperature oils – 49% - 0.855 g/cm3.
The cost of electricity to process one ton of coal from grinding to the finished product is 50-70 kW/h.
The cost of one ton of finished fuel (gasoline, diesel, low-temperature oils) is 50-100 euros (depending on the cost of raw materials).
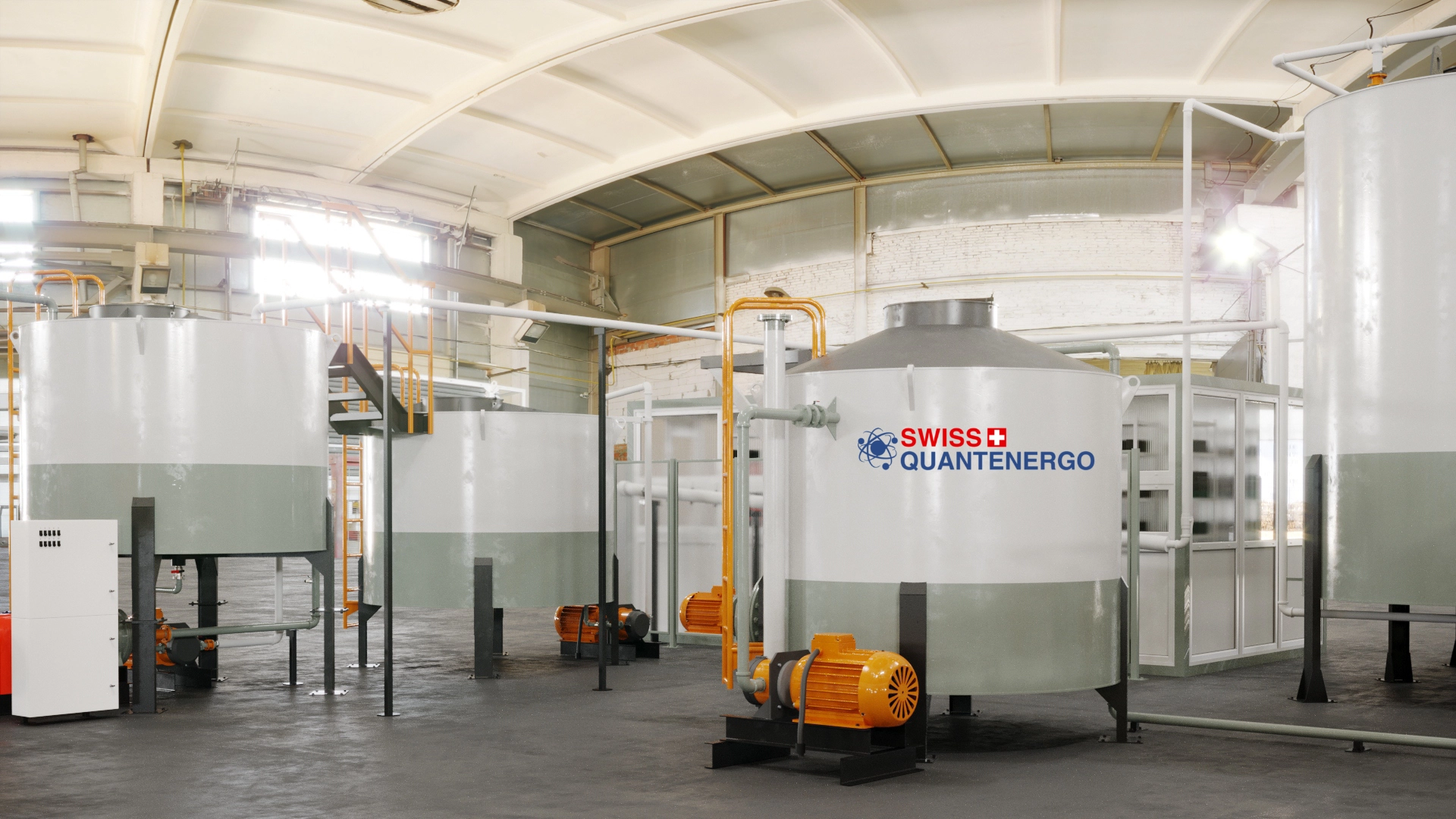
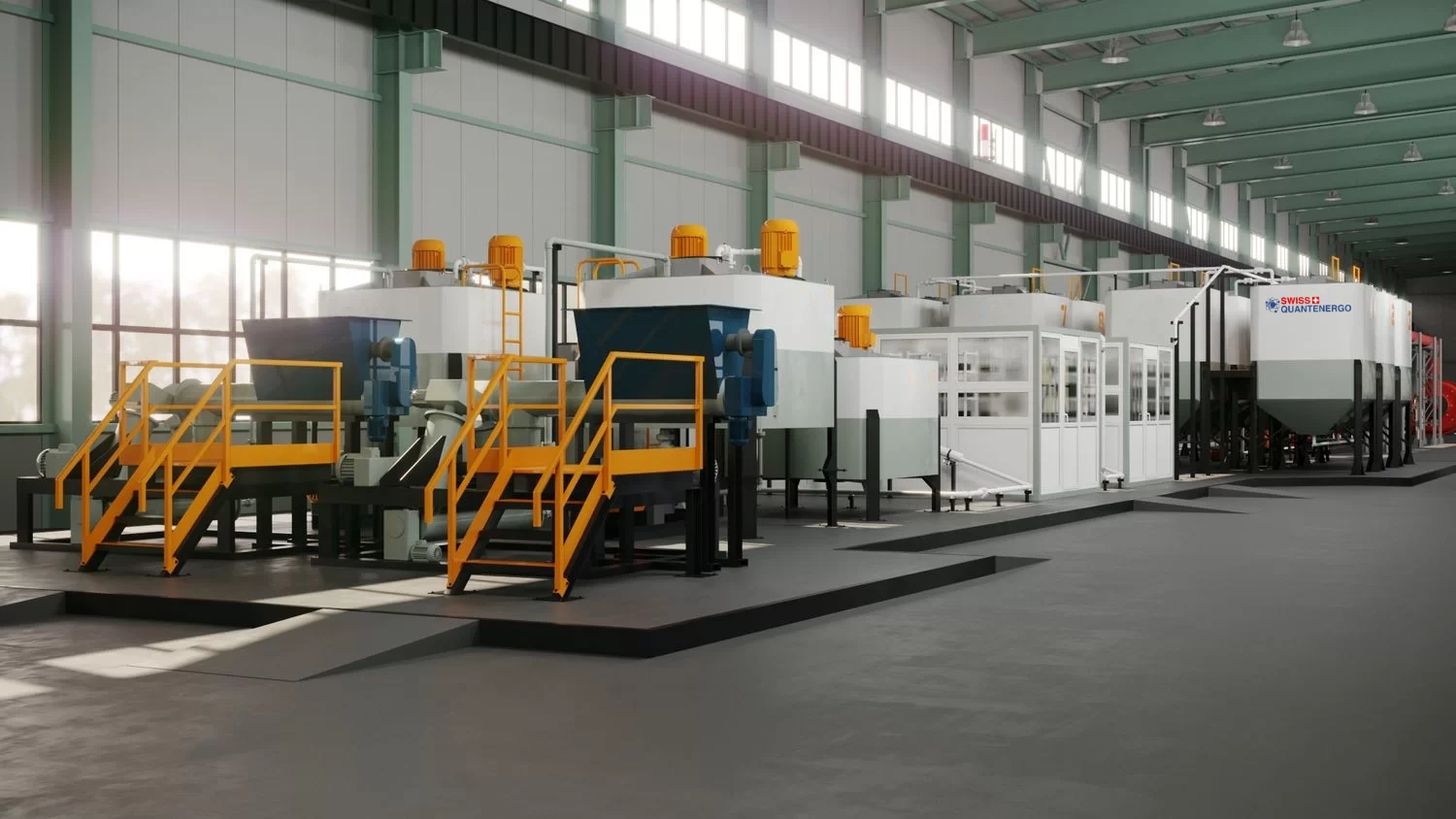
PROCESS TECHNOLOGY
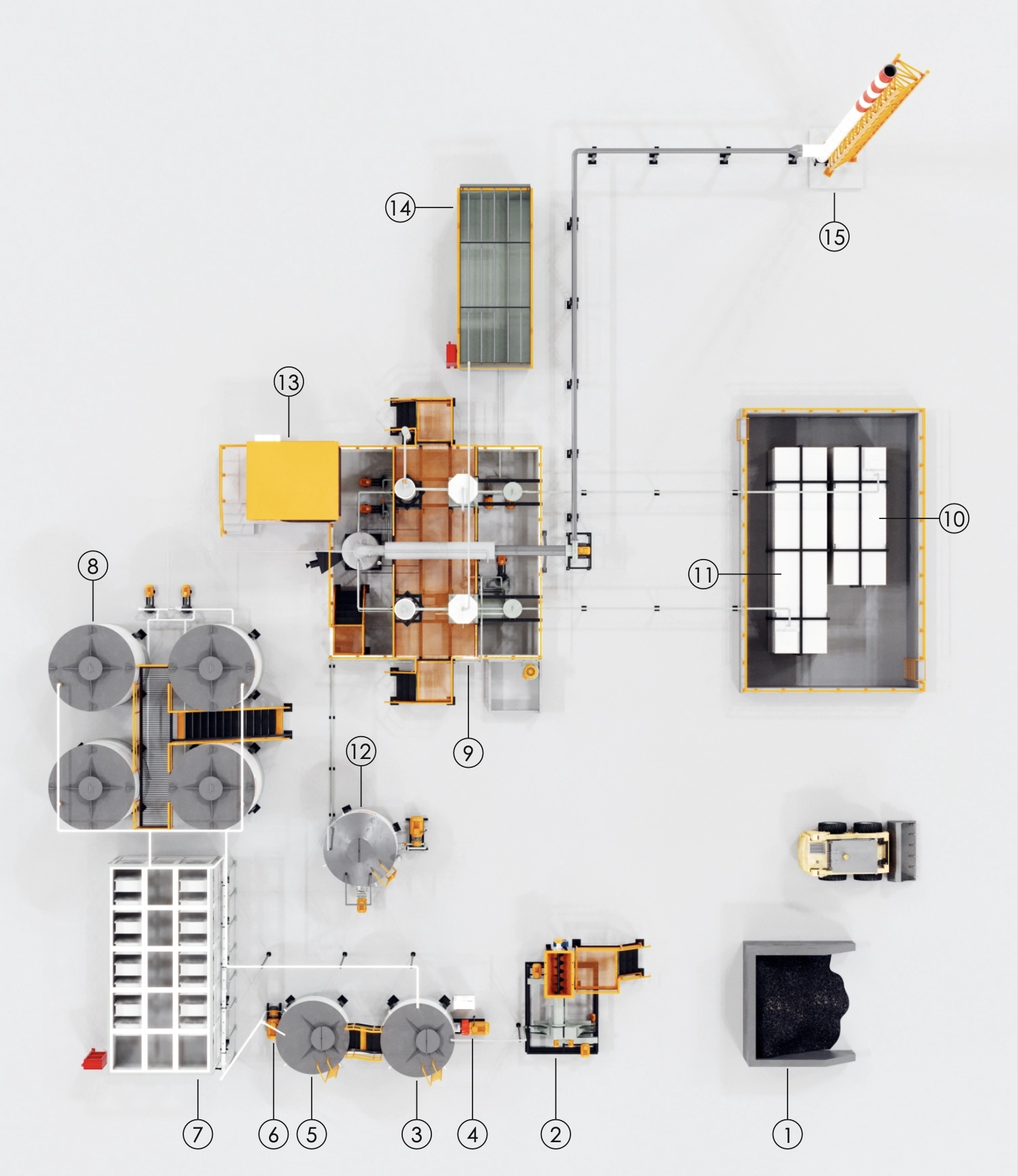
The initial coal (1) is ground in a wet grinding disintegrator (2) to particles sized from 0.1 to 0.3 mm. For wet grinding, one ton of coal requires 600 to 750 liters of water, which is dosed onto the ground coal through a sprayer. The resulting water-coal emulsion with a density of 1.3 kg/m3 is sent to a container (3) for mixing it with an organic solvent. To one ton of processed coal (depending on its brand) from 250 to 400 liters of organic solvent are added. Cavitation hydraulic impact coal disperser (4) provides even finer grinding of coal to 0.003-0.01 mm, mixes and homogenizes the mixture of coal, water and organic solvent. The maximum access of the organic solvent-activator to the coal particles is insured in the circulation mode of the cavitator-disperser at a rotational speed of 3000-12000 rpm, resulting in a homogeneous emulsion. The process of circulation through the cavitator-disperser is thermal (a homogeneous emulsion heats up when passing through it). The prepared homogeneous emulsion from the tank (3) is fed into the storage tank (5), from where it is pumped (6) to the upper part of the plasma-chemical reactor (7), where a local (point) effect of a high-voltage plasma pulsed discharge occurs. In a high-voltage plasma pulsed discharge, coal particles of a homogeneous emulsion are ground to a nano-size. Molecules of coal are saturated with hydrogen and oxygen in the presence of a hydroxyl group •OH radical under the influence of a high-voltage plasma discharge in a strong electromagnetic field during a plasma-chemical reaction. The transmutation of the substance occurs, new interatomic and intermolecular substances are formed, there is transition to a liquid (liquefied) state. The resulting primary synthetic oil enters storage tanks (8). Next, the primary synthetic oil enters the plant (9) for its processing into straight-run gasoline, diesel fuel, low-temperature oils.
DOCUMENTS FOR DOWNLOAD
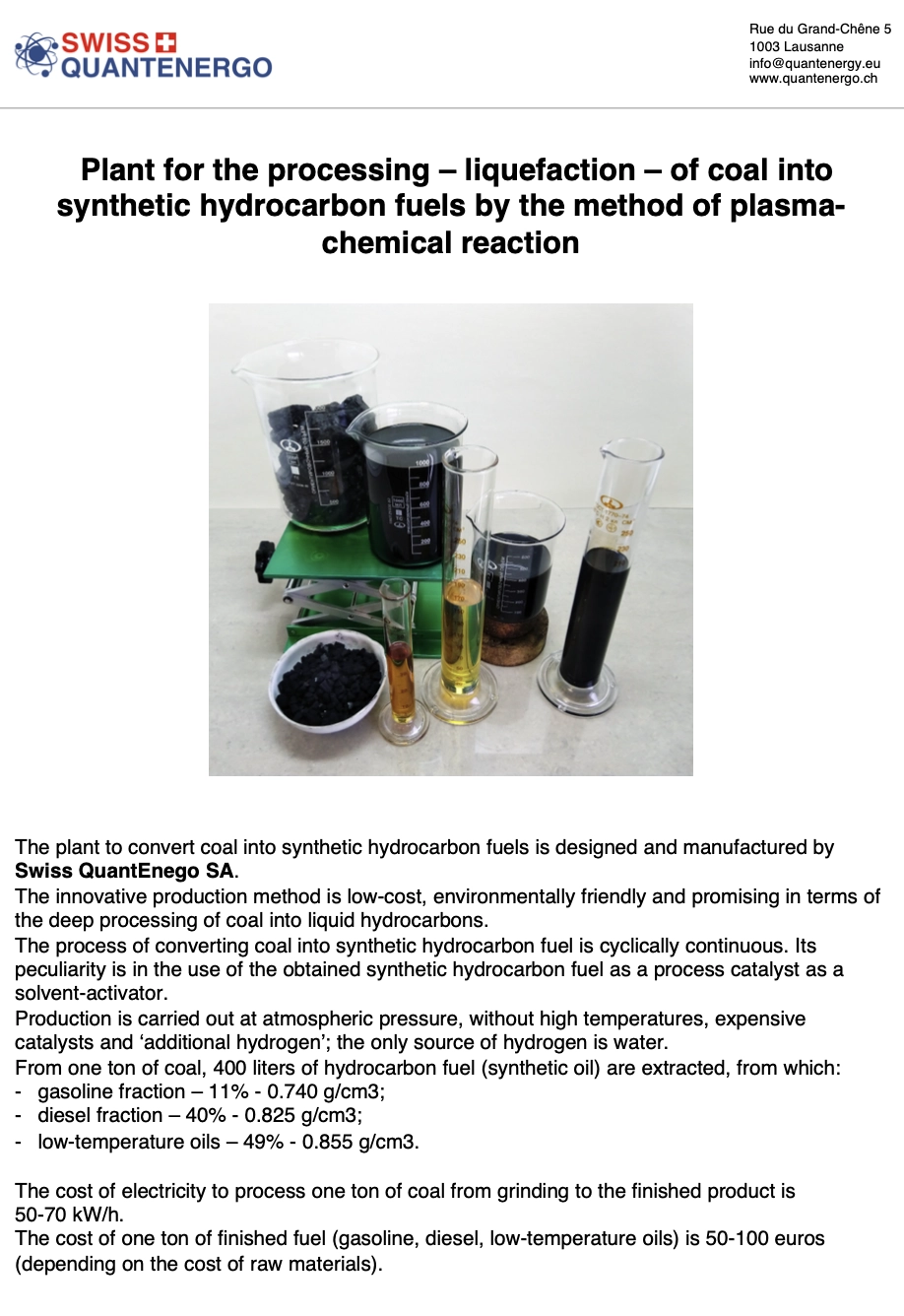
Our Brochure in English
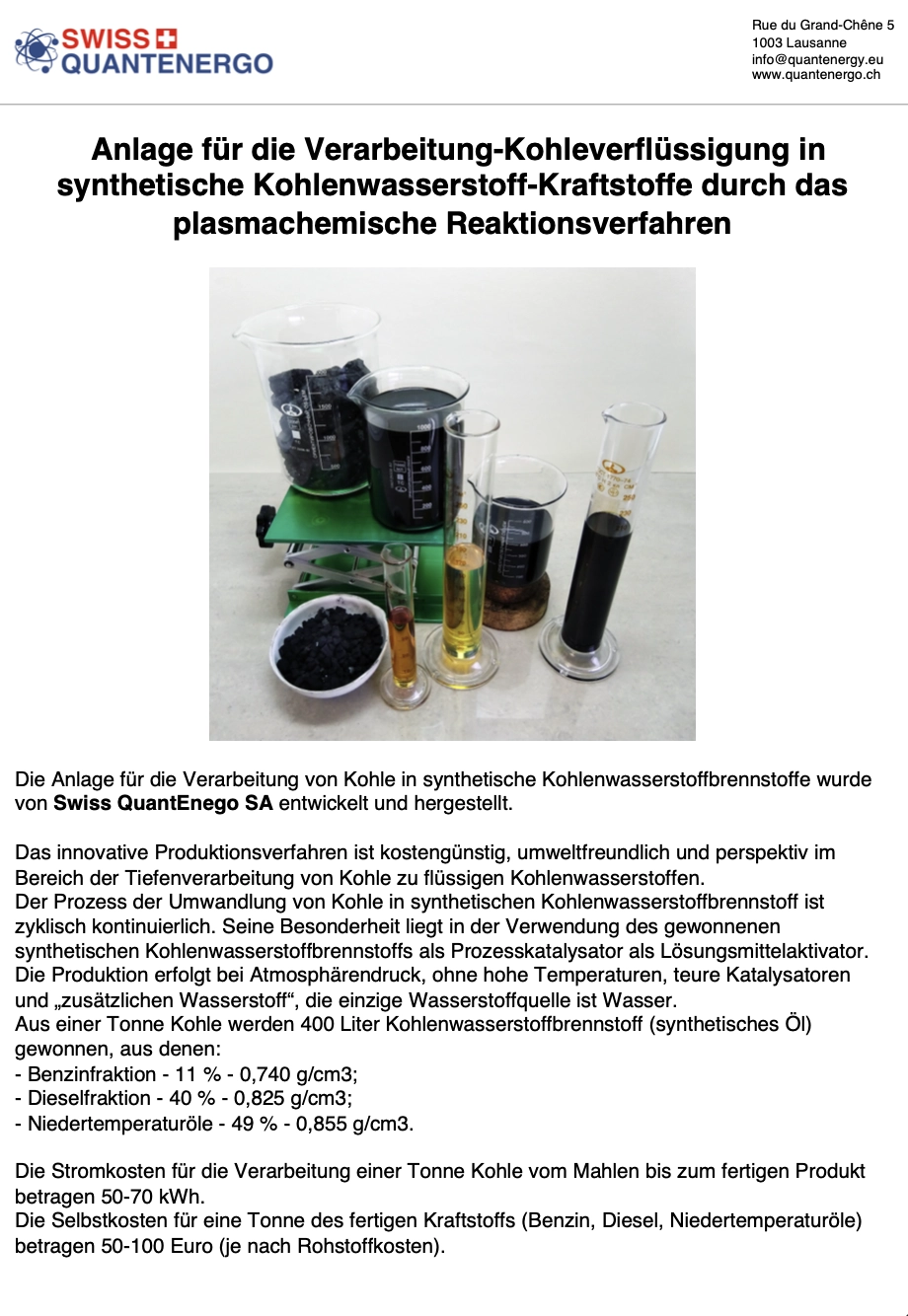